Проблемы качества. Возвращаясь к теме...
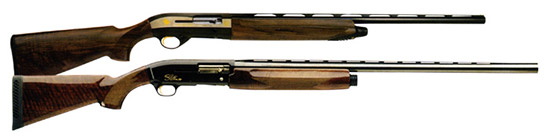
Делая ствольную коробку гладкоствольных самозарядок «легкосплавной», конструкторы частенько забывают об ударных нагрузках, возникающих при откате затвора и его ударе о казённую часть коробки. Итог - разбитые амортизаторы отката затвора у Beretta AL391 Urika или Browning Gold Hunter и даже сколы металла на внутренней поверхности ствольной коробки.
Cтало почти нормой применение на самозарядном и «помповом» гладкоствольном оружии ствольных коробок из сплавов на основе алюминия. Причина - лёгкость обработки, доступность и дешевизна материала. Введя в конструкцию оружия, имеющего неподвижный ствол, сцепление затвора непосредственно со стволом, казалось бы можно и «разгрузить» почти «ненужную» теперь затворную коробку. Ну и разгрузили, сделав её «лёгкой». Но не все конструкторы учли ударные нагрузки, возникающие при откате затвора и его ударе о заднюю часть затворной коробки у гладкоствольных «самозарядок». Мне известно о двух десятках вдребезги разбитых амортизаторов отката затвора у Beretta AL-391 Urika и о почти стольких же у Browning Gold, Hunter, Fusion. В половине этих случаев имелись серьёзные наклёпы и даже сколы металла на внутренней поверхности затворной коробки.
Стальные коробки на гладкоствольном самозарядном и «помповом» оружии ныне, похоже, только у Remington. Стальная ствольная коробка и у самозарядного ружья Cosmi - но это «птица очень высокого полёта».
Стальные ствольные коробки на самозарядном нарезном оружии встречаются теперь только на некоторых исполнениях Browning BAR II, у Benelli Argo и, пожалуй, всё. Почти у всех остальных моделей такого оружия ствольные коробки скомбинированы из стальных и «легкосплавных» деталей.
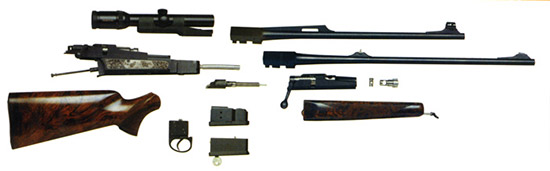
А теперь о разнице между стальной и легкосплавной ствольными коробками, даже в том случае, когда затвор сцепляется непосредственно со стволом.
Лично видел и осматривал три экземпляра Remington 870 с разрывами патрона на лотке подавателя непосредственно в ствольной коробке. Итог: УСМ разрушен неисправимо; из магазинной трубы «выплюнуло» всё содержимое вперёд, как из ствола (сорвав с резьбы при этом крышку магазина). НО: затвор цел, ствол цел, ствольная коробка только слегка раздута и подлежит восстановлению.
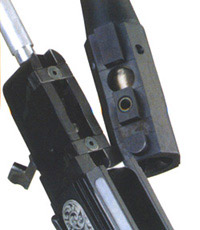
Два экземпляра Browning Gold с аналогичными проблемами. УСМ разрушены непоправимо, стальные магазинные трубки целы (теперь они тоже легкосплавные), затворы и стволы целы. Ствольные коробки выдержали, но были раздуты с сильными деформациями и не подлежали восстановлению.
Не менее шести экземпляров дешёвых «помповых» ружей 12-го калибра фирм Germanica и S.P.A.S.S. с поперечными трещинами ствольных коробок, соединяющими «выводное» и «загрузочное» окна, причём у половины из ружей трещины наблюдались и на левых щеках ствольных коробок. Все остальные детали, узлы и сборки оружия были вполне в сносном состоянии; пострадали только ствольные коробки.
Есть ещё одна «сложность» с легкосплавными ствольными коробками. Инженеры-технологи, видно, посчитали возможным пренебречь фактом, что коэффициент трения «сталь по стали» меньше, чем «сталь по алюминию». Следовательно, для оружия со стальным скользящим затвором и легкосплавной коробкой смазка ещё более важна, чем для оружия со стальной коробкой. При попадании пыли (а пыль - абразив) в ствольную коробку на хотя бы слегка смазанные поверхности, в том числе затвор, получается, что последний ведёт себя в ствольной коробке как стальной притир, смазанный абразивный пастой. Отсюда быстрое изменение шероховатости поверхностей внутри ствольной коробки из «лёгкого» сплава, изменение размеров, ускоренный износ и т.д. В стальных ствольных коробках эти процессы протекают существенно медленнее...
Единственно, где «держатся» стальные ствольные коробки, - это магазинные винтовки и карабины с продольно-скользящим затвором. Надо сказать, и здесь появились «отступники», например, винтовка Bix Andy, имеющая легкосплавную ствольную коробку, но, правда, со стальным вкладышем-втулкой внутри, Chapuis Challenger и другие.
Всё чаще находит своего покупателя т.н. «облегчённое» оружие с откидными стволами: одно-, двух- и даже трёхствольное. Конечно, колодки там усилены, «где надо», стальными вкладышами, но «чего не понимаю - того не одобряю» (что это за оружие, колодку которого можно поцарапать ногтем?).
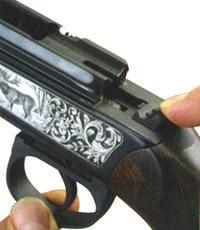
Трудно, что называется, «с ходу» перечислить наиболее часто встречающиеся модели гладкоствольного «помпового», самозарядного нарезного и гладкоствольного оружия, у которых спусковые механизмы оформлены в один блок и легко вынимаются из ствольной коробки при удалении одной или двух шпилек. Корпуса этих механизмов большей частью выполняются из сплава на основе алюминия. Эти сплавы хорошо держат форму, хотя всё-таки мягки. Но всё чаще изготовляют корпуса спусковых механизмов, отливая их из пластических масс. Наиболее характерный пример - Beretta AL-391 Urika. То ли размеры подобраны неверно, то ли усадка у пластмассы «не та», то ли при остывании отливку «ведёт» - не знаю, но у большинства экземпляров этой модели спусковые механизмы с трудом покидают при разборке ствольную коробку и с таковым же ставятся на место.
Пластмассы, как правило, плохо держат штифы и оси, отличаются колкостью, на их поверхностях легко возникают задиры, намины и т.д.; наибольшая беда корпусных деталей из пластмасс -трещины, выколы или разрушение внутренних перегородок и других тонкостенных элементов. Словом, корпуса спусковых механизмов, выполненные из пластических масс, ведут себя существенно хуже, чем изготовленные из других сплавов на основе алюминия. К тому же они более чувствительны к загрязнению.
Наблюдал два разрушенных корпуса спускового механизма от Beretta AL-391 Urika, один - Winchester 1300; один - Mossberg 9200; один - Maverick и один - единственный легкосплавный корпус спускового механизма, вышедший из строя, и то на стареньком советском МЦ 21-12...
Всё шире применяется в производстве оружия такой приём изготовления деталей, как «порошковая» металлургия. Я не буду вдаваться в особенности этого прогрессивного метода, но замечу, что хоть оборудование для его реализации и дорогостоящее, но быстро себя окупающее: детали получаются с очень высокой степенью готовности и практически не нуждаются в доводочных операциях. Детали могут изготавливаться из порошков различных металлов с соответствующими каждому конкретному случаю добавками. Один недостаток: весьма часто детали получаются с такой высокой степенью твёрдости, что с трудом берутся «алмазными» надфилями - напильники просто «отдыхают». Обычно свёрла и фрезы их тоже не берут - требуется специальный инструмент. Но обратная сторона твёрдости - хрупкость: эти детали не выносят изгибов, ударов и т.п. Этим методом иногда изготавливаются выбрасыватели, затворные рамы, тяги, рычаги взведения, шептала, спусковые крючки, интерсепторы (перехватыватели), курки, отражатели и другие детали, не являющиеся телами вращения и обыкновенно бывающие «клиентами» фрезерного станка. Бесполезно эти детали гнуть, рихтовать, «оттягивать»: они ломаются, крошатся. Очень трудно их наваривать.
Для оружия со стальным затвором и «легкосплавной» коробкой смазка более важна, чем для оружия с чисто стальной коробкой. В мире болтовых магазинных винтовок и карабинов стальные ствольные коробки пока не сдают своих позиций. Хотя, и здесь появились «отступники» - например, винтовка Chapuis Challenger.
Разрыв в качестве между добротным охотничьим оружием и «валовым», рядовым, увеличивается с каждым годом. Что остаётся отечественному покупателю? Брать качественное оружие сейчас, пока оно ещё есть и доступно по цене. И избегать по возможности ныне модных «облегчённых» вариантов оружия...
Эти детали - головная боль ремонтника.
Невозможно не упомянуть о крепежных изделиях, применяемых на современном оружии. Если раньше каждая оружейная фирма имела свои заводские стандарты на крепёжные изделия: свои резьбы, свои оси, винты, штифту, втулки, шайбы, гайки, шплинты, шурупы (причём, бывало, какая-нибудь модель могла иметь свой уникальный крепёж), то теперь всему этому разнообразию пришёл полный и окончательный... эээ... конец. Практически все фирмы-изготовители оружия (за исключением, пожалуй, самых «родовитых», да и те уже «на подходе») перешли на крепёжные изделия общетехнического в самом широком смысле этого слова, назначения, т.е. «на револьвер ставят гайку от паровоза». Разберите пару импортных стиральных машин, кофеварку какую-нибудь размером побольше и ещё что-то из «бытовухи» и вы обнаружите те же самые саморезы, те же винты с головкой под Г-образный шестигранник, те же запорные шайбы и много прочей мелочи, причём зачастую в тех же самых типоразмерах, кои применяются в современном иностранном оружии. И материалы почти те же, за исключением ствольной стали.
Это говорит не только о стандартизации и унификации крепёжных изделий в пределах целой страны или даже группы стран, такая унификация сама по себе - дело правильное и благое. Всё это было когда-то у нас (знаменитые ГДСТы СССР и Стандарты СЭВ), только не доводилось до глупости: на оружейный крепёж были свои СТП - стандарты предприятия, и не шире того. Это свидетельствует в первую очередь о серьёзном сокращении расходов при изготовлении оружия фирмой-производителем, оптом закупающей крепёж на стороне. А вот какого качества данный крепёж - это уже большой вопрос, ибо отследить качество покупного крепежа фирме-покупателю куда труднее, чем качество «своих» деталей. Смею заверить: от качества крепёжных изделий напрямую зависит качество всего изделия. Зависимость линейная. Изготовление крепёжных изделии к оружию должно находиться в руках фирмы-изготовителя оружия - в этом заключается первая ступень в достижении высокого качества оружия! И только так!
Ситуация: одна хорошая небольшая немецкая фирма, производящая охотничье оружие, перешла на DIN-овский крепёж (DIN-это свод германских стандартов). В спусковом механизме двуствольного дробовика используются стандартные DIN-овские оси. В одном месте применяется слишком короткая ось, и она произвольно «гуляет» в проушинах колодки, сдвигаясь то вправо, то влево. В своих крайних положениях она упирается в дерево щёк шейки приклада и, естественно, покинуть колодку не может. Но при этом она покидает одну из проушин, и её конец занимает положение прямо посередине между проушинами. Но между ними на этой оси сидит с соответствующими зазорами двуплечный рычаг, совершающий качающиеся движения - типа коромысла. В таком положении, когда рычаг сидит только на половине оси. его неизбежно перекашивает и клинит - то вправо, то влево.
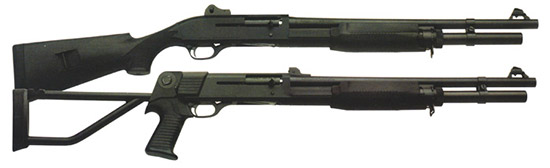
При эксплуатации или ремонте оружия нередки и проблемы с крепежом. Так, заменить приклад на рукоятку с откидным плечевым упором у итальянской гладкостволки Benelli МЗ Super 90 бывает очень сложно. Попытки отсоединить эти узлы от ствольной коробки без предварительного воздействия на синтетический клей, который «держит» резьбу винтов, ни к чему хорошему не приводят.
Во: куда ось уйдёт. Выход из положения простой - применить более длинную ось того же диаметра. А следующий размер по длине осей этого диаметра по DIN - на 1 или 2 мм длиннее, чем надо, т.е. такая ось будет выступать за пределы колодки и мешать садиться дереву ложи на своё место.
На предложение применять длинную ось и при сборке оружия опиливать эту ось, доводя её до нужной длины, было подчёркнуто, что это-де «лишняя операция» (!) и что «ось тогда будет нестандартной». В результате оружие получило ещё одно слабое место в спусковом механизме; эта потенциальная неисправность время от времени даёт о себе знать. «Лечится» она просто - при помощи обыкновенного русского гвоздя: ему, гвоздю, на DIN наплевать.
Всё это, как говорится, ещё полбеды. Ну и чёрт с ним, с этим общетехническим крепежом, держал бы - и то ладно. Но, во-первых, «держит» не всегда, а, во-вторых, всё чаще применяются виды крепежа и приёмы сборки, которые не рассчитаны, похоже, даже на однократную разборку с последующей сборкой. Шлицы винтов, шурупов и саморезов, грани «под ключ» часто разбиваются при первой же разборке, стопорные «лепестковые» шайбы теряют свои «лепестки», свивные (свёрнутые из тонкого листового металла, подобно свитку) штифты и так не любят многократного использования, а тут ещё стопорение резьбы всякими клеями, красками и лаками. Есть, правда, и «перегибы» в другую сторону: саморезы, входящие в комплект для установки антабки на ствольный блок ружья Beretta 686, сплошь и рядом закалены столь сильно, что при затягивании «теряют голову».
Целый ряд узлов, соединяемых между собой при помощи резьбы или с помощью винтов, теперь «контрится» от самоотворачивания «соплями» - быстротвердеющим синтетическим клеем, который держит резьбу «мёртво». Это следующие соединения: трубчатого корпуса возвратного механизма с тыльной частью ствольной коробки у Beretta AL-391 Urika, у Benelli Raffaello и др.; трубки крепления приклада с тыльной частью ствольной коробки у Benelli Super 90; магазинной трубы (корпуса магазина) со ствольной коробкой уBeretta AL-391 Urika, Benelli Raffaello, Benelli M1, M3 Super 90, Browning Gold и др., винт крепления спускового механизма у Blaser R 93 и т.д..
При эксплуатации и особенно при ремонте нередки случаи, когда возникает необходимость полностью демонтировать возвратный механизм или магазин. Или заменить приклад на рукоятку с откидным плечевым упором (Benelli МЗ Super 90), или произвести техническое обслуживание спускового механизма (Blaser R 93). Попытки отсоединить эти узлы от ствольной коробки (колодки) без предварительного воздействия на клей ни к чему хорошему не приводят. Попытки размягчить его каким-либо растворителем не помогают. Единственное, по моим сведениям, что этот клей берёт, так это прогревание пламенем газовой горелки...
Но, применяя растворители, можно повредить покрытие легкосплавных ствольных коробок - кто его знает, чем их мажут при изготовлении: восстановить повреждённые покрытия в «домашних» условиях явно не удастся. Греть же ствольные коробки и тонкостенные трубки - явное варварство. Во-первых, может быть повреждено то же самое покрытие, во-вторых, при локальном нагреве тонкостенных деталей возникают местные напряжения и деформации - причём несимметричные; в-третьих, никто не знает, как поведёт себя после остывания главное действующее лицо - ствольная коробка: не возникнут ли в ней микротрещины.
«А что же советуют фирмы-изготовители?» - спросит читатель. А ничего не советуют! «Фирмы» хранят гордое молчание. Их это не касается. Например, господа из Browning на вопрос, «чем размягчить клей», ничего не ответили. Они вообще ни на один вопрос толком ничего не сказали. А на вопрос: для чего в газовом двигателе самозарядного карабина BAR II применяется подпружиненное инерционное тело (деталь №38, код ВЗ17677003, inertia piece) «фирмачи» гордо ответили: «Потому, что так придумано!»
Итак. Качество конструктивных решений, применяемых при проектировании нового зарубежного оружия, явно не столь высокое, чтобы пасть перед ним ниц; качество применяемых материалов (за исключением ствольных сталей) явно понизилось; качество комплектующих - тоже; качество сборки упало. Налицо ухудшение качества иностранного охотничьего оружия, но если понизилось качество, неизбежно понизится и долговечность. За стволы пока можно не особо беспокоиться, но механизмы износятся быстрее стволов. Всё, конечно, зависит от настрела и от ухода за ружьём, но, по неофициальным данным, иностранное гладкоствольное ружьё «валового» производства рассчитано на 10-15 лет довольно «вялой» западной эксплуатации. Я думаю, этот срок можно смело сократить вдвое при эксплуатации этого оружия в наших условиях.
Какие напрашиваются выводы из изложенной в статье информации, какие прогнозы на ближайшее время можно составить?
В самое ближайшее время (10-15 лет):
- Качество «валового», рядового иностранного охотничьего оружия будет только ухудшаться, а его количество - увеличиваться.
- Количество крупных фирм-производителей охотничьего оружия будет сокращаться. В том числе за счёт их слияния и укрупнения, но это не скажется на общем количестве выпускаемого оружия.
- Число мелких и небольших фирм, выпускающих хорошее оружие, будет неминуемо сокращаться, количество же производимого ими оружия как минимум не может резко возрасти без ущерба для его качества, поэтому почти наверняка будет ограничено.
- Разрыв в качестве между добротным оружием и «валовым», рядовым охотничьим оружием будет только расти.
- Среди мелких производителей оружия (кустарей и штучников), владеющих оружейными мини-фирмами, выпускающими оружие высочайшего класса, уже сейчас происходит расслоение. И в дальнейшем оно будет ещё большим, так как не все смогут удержать высокое качество производимого оружия. Велик соблазн использовать простые, доступные, дешёвые и менее длительные технологии взамен «дедовских», не все могут себе позволить отказаться от применения относительно дешёвых покупных узлов и комплектующих изделий. Настоящий «штучник», настоящий мастер-универсал станет очень редок.
- Крайне небольшое количество фирм-изготовителей оружия самого высокого класса, имеющих вековые традиции, уменьшится, качество выпускаемого ими оружия будет понижаться, но зато увеличится его количество.
- На рынке охотничьего оружия возрастёт количество «конверсионного» оружия и «гражданских» версий военного оружия.
- Гарантийный срок фактически уже поменял своё назначение: из гарантированного изготовителем срока безотказной работы оружия он превратился в срок пробной эксплуатации (обкатки) оружия, в течение которого изготовитель через свой сервисный центр обязуется бесплатно устранять все выявленные неполадки. Такое положение вещей постепенно станет нормой.
Что можно посоветовать отечественному покупателю охотничьего оружия? Приобретайте добротное и качественное оружие сейчас, пока оно есть и доступно по цене. Рискну посоветовать обратить внимание на продукцию фирм Merkel, Heym, Anschutz, Sako, Sauer, но избегайте ныне модных «облегчённых» вариантов оружия.
Кстати, народ вновь потянулся в оружейные «комиссионки», выискивая старые «меркели» и «браунинги авто пятые», «геймы» и «генели», «грейфельты» и «геко», довоенные Бельгию и Францию, невзирая на подчас сильно изношенное состояние.
И вопрос последний. Что могут сделать в создавшейся ситуации отечественные заводы-производители охотничьего оружия? Они могут этой ситуацией успешно воспользоваться. Не является государственным секретом, что охотничье оружие у нас выпускается в огромном большинстве случаев по «устаревшим» технологиям и на старом оборудовании. Это, конечно, плохо, но одновременно и хорошо. Это оборудование и технологии рассчитаны на применение добротных, качественных материалов, какие уже почти не применяются на Западе. Ведь у нас даже газобаллонный пневматический пистолет Макарова выпускается из хорошей оружейной стали. Следовательно, одна составляющая хорошего качества уже есть и, судя по всему, ещё долго будет присутствовать. Следует также учесть, что у нас весьма мало применяется при изготовлении деталей метод «порошковой» металлургии, нет столь широкого использования пластических масс, какое существует «за границей», у нас отсутствует сборка в «третьих» странах, нет заокеанских комплектующих. В то же время наши конструкторские кадры превосходят своих «западных» оппонентов. Это второе составляющее качества.
Чего не хватает? Культуры производства, утраченной за годы «перестройки». Пример. Ружьё ИЖ-27. За границей его система считается одной из самых надёжных в мире, а изготовление - одним из самых худших. И действительно, его будто топором рубили, один приклад чего стоит. А ведь запросто ружьё можно «дотянуть» до нынешнего Merkel модель 2000. Вопрос даже не в технике - вопрос в людях, которых надо научить правильно работать, и вообще сделать аккуратную и качественную работу очень прибыльным делом.
Давайте попробуем?
Константин Грау
МастерРужьё, 11(140) - 2008
- Статьи » Дробовики
- Mercenary48350
Комментарии
Добавлять комментарии могут только зарегистрированные пользователи